The Silent Guardian of Your Wheels: Unraveling the Enigma of Torque Settings
Imagine a world where the simple act of driving held a hidden, potentially dangerous secret, lurking beneath the sleek exterior of our vehicles. This hidden danger lies in the seemingly mundane wheel nuts, those small but mighty fasteners that hold our wheels securely in place. The key to unlocking their full protective potential lies in understanding and applying the correct torque settings for wheel nuts, a critical aspect of vehicle safety often overlooked.
Proper wheel nut torque is not merely a mechanical procedure; it's a precise science that balances the forces acting upon the wheel assembly. Incorrect torque can lead to a cascade of problems, from loose wheels and vibrations to warped rotors and even catastrophic wheel detachment. Understanding the nuances of this seemingly simple task can be the difference between a smooth, safe journey and a potential disaster.
The history of torque settings for wheel nuts is intertwined with the evolution of the automobile itself. As vehicles became faster and more complex, the need for precise and consistent fastening methods became paramount. Early automobiles relied on rudimentary tightening methods, often leaving wheel security to the subjective judgment of the mechanic. The introduction of torque wrenches marked a significant advancement, allowing for accurate and repeatable tightening, thereby enhancing safety and reliability.
The importance of correct wheel nut torque stems from the delicate balance of forces at play. Over-tightening can stretch or damage the wheel studs, leading to premature failure. Under-tightening, on the other hand, allows the wheel to loosen gradually, potentially causing vibrations, uneven brake wear, and even complete wheel separation. Maintaining the proper torque ensures that the wheel is securely attached without undue stress on the components.
The primary issue surrounding wheel nut torque is the lack of awareness and understanding among drivers. Many are unaware of the specific torque requirements for their vehicle or the importance of using a calibrated torque wrench. This often leads to improper tightening, increasing the risk of wheel-related incidents. Complicating matters further is the variation in torque specifications across different vehicle makes and models, highlighting the need for readily available and accurate information.
Torque, in the context of wheel nuts, refers to the rotational force applied to the nut. It is measured in units such as pound-feet (lb-ft) or Newton-meters (Nm). The correct torque setting ensures that the clamping force between the wheel and the hub is optimal, preventing loosening or over-tightening. For example, a typical passenger car might require a torque setting of 80-100 lb-ft, but this value can vary significantly depending on the vehicle.
Implementing correct wheel nut torque offers several benefits. First, it enhances safety by preventing wheel detachment. Second, it improves vehicle handling and stability by ensuring proper wheel alignment. Third, it prolongs the lifespan of wheel studs and other components by preventing stress and damage.
To ensure proper wheel nut tightening, follow these steps: 1) Consult your vehicle's owner's manual for the correct torque specification. 2) Use a calibrated torque wrench. 3) Tighten the nuts in a star pattern to distribute the clamping force evenly. 4) Recheck the torque after driving a short distance.
Advantages and Disadvantages of Correct Torque Settings
Advantages | Disadvantages |
---|---|
Increased Safety | Requires specific tools (torque wrench) |
Improved Handling | Requires knowledge of correct specifications |
Extended Component Life | Can be time-consuming if not practiced |
Five best practices: 1) Use a calibrated torque wrench. 2) Follow the star pattern. 3) Re-torque after driving. 4) Clean the threads. 5) Consult your owner's manual.
Five examples of torque settings: 1) Passenger car: 80-100 lb-ft. 2) Light truck: 100-140 lb-ft. 3) SUV: 90-120 lb-ft. 4) Motorcycle: 40-60 lb-ft. 5) Trailer: 90-110 lb-ft. (Note: These are examples only, always consult your owner's manual.)
Five FAQs: 1) What is torque? 2) Why is it important? 3) What happens if I over-tighten? 4) What happens if I under-tighten? 5) How often should I check?
In conclusion, the seemingly small detail of proper wheel nut torque holds immense significance for vehicle safety and performance. By understanding the principles of torque, utilizing the correct tools and techniques, and adhering to recommended practices, we can safeguard ourselves and others on the road. The meticulous attention to this often-overlooked aspect of vehicle maintenance is a testament to our commitment to safety and a reflection of the intricate engineering that underpins modern transportation. Embracing this knowledge empowers us to take control of our vehicle's well-being and ensures a smoother, safer, and more confident driving experience.

Proper Torque For 34 Lug Nuts | Kennecott Land

Torque Settings for Wheel Bolts Wheel Nuts | Kennecott Land
Torque Spec Chart For Lug Nuts | Kennecott Land

Lug Nut Torque Specs 5th Wheel Rv | Kennecott Land

2017 Mitsubishi Outlander Lug Nut Torque Spec | Kennecott Land

Audi Wheel Nut Torque Settings | Kennecott Land

Torque Settings for Wheel Nuts | Kennecott Land
Hub Bolt Torque Specs at Thomas Stephens blog | Kennecott Land

Printable Lug Nut Torque Chart | Kennecott Land

Torque Specs For Wheels Lugs | Kennecott Land

Truck Lug Nut Torque Chart | Kennecott Land

Lug Nut Torque Specifications | Kennecott Land
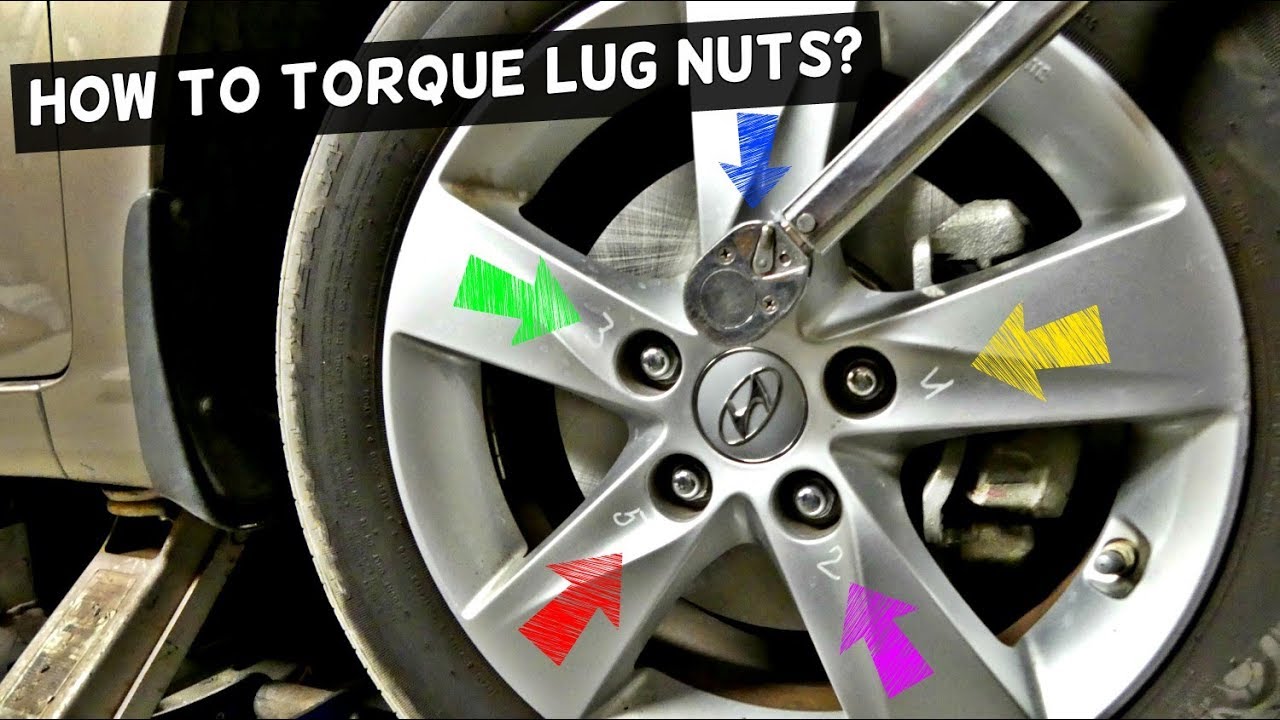
Torque Specs For Truck Lug Nuts | Kennecott Land

Wheel Nut Torque Specifications Chart | Kennecott Land

Torque Specs Wheel Lug Nuts | Kennecott Land